One of the biggest threats to utility personnel working on or near a roadway is a vehicle crashing into the work zone. More than 279 times each day, or 102,000 times in 2021, a crash occurred in a work zone. Of the 156 pedestrian fatalities occurring in work zones, 32% were workers. We asked two utility companies recognized for outstanding safety how they manage this risk.
1. Plan for safety
When working adjacent to a highway, safety executives at South Carolina-based Santee Cooper like to plan for the operation whenever possible. A version of the federal Manual on Uniform Traffic Control Devices (MUTCD) guides the setup of safe work zone layouts. It includes detailed schematics and examples of recommended advance traffic control warning signs, tapers for lane transitions, buffer spaces, temporary channelizing devices (such as cones, drums, traffic barriers), and pavement markings.
“We try to do as much planning as possible to mitigate issues,” says Rose Foster, Safety Specialist for Santee Cooper, who is responsible for the safety of 14 crews working in Myrtle Beach, SC. When emergency repairs are needed, the utility will often work with law enforcement agencies to divert traffic.
Risks increase with higher speeds and more traffic. “If we can, we like to close the lane,” says Foster. Vehicles are parked on the road, where they can serve as an obstacle to prevent oncoming traffic from hitting workers in the work zone.
“The number of controls put in place will vary depending on the situation, whether it’s a rural road with little traffic or an urban area with a lot of traffic,” says Tony Long, Director of Safety & Health Services at JEA, a community-owned electric, water and sewer utility based in Jacksonville, Florida. “Both are equally important. It only takes one vehicle to create a devasting life-altering event.”
“The projects that we know in advance, we plan for,” adds Long. “We have planners and project managers, foremen, and crew leaders who will plan out what needs to happen.”
2. Get visible
High visibility clothing and equipment mitigates risk in the work zone. Santee Cooper utilizes Class 3 safety gear along with yellow flashing signs behind the vehicle and overhead lights on trailers when working at night. “We use strobes in our headlights and taillights and rotating strobes on the roof of the vehicles,” says Jason Fugate, Senior Manager of Occupational Safety and Health at Santee Cooper. White vehicles with reflective tape improve visibility. JEA also utilizes highly reflective PPE and portable lighting when working at night.
3. Improve awareness and keep an eye on the traffic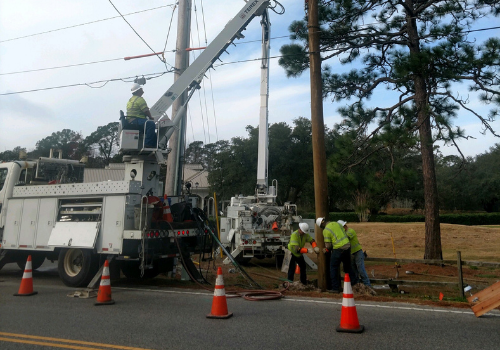
JEA relies on classroom and on-the-job training to teach workers the hazards of working near or on a roadway. “We discuss what we need to keep each other safe,” says Long. “We teach workers to be aware of their surroundings, to pay attention to signs and alarms, and to stay focused.”
JEA gives special emphasis to new-hire training and pairs new workers with a more experienced co-worker to mitigate the risk that comes with inexperience.
“When working near a roadway, awareness needs to be heightened,” says Foster. At Santee Cooper, the crew supervisor watches the workers and the traffic. The flagger always has his eyes on the oncoming traffic. “As a worker, your head needs to be on a swivel,” she says.
4. Engage workers in safety
Fugate believes keeping workers safe in any situation requires ongoing engagement. Over the past four years, Santee Cooper has focused on continuous improvement. “We’re always looking for what’s next,” says Fugate. “We’re doing more risk assessments, more training, we’re updating our people on where we are with safety.” The end result is a low safety incident rate that has earned them recognition by the American Public Power Association for several consecutive years.
JEA is proactive in observing workers and coaching to avoid at-risk behaviors. When things are done right, those behaviors are reinforced. Long believes consistency in messaging contributes to their success. “We have a standing call with our directors every Monday morning where we discuss near misses and/or incidents as well as corrective action,” says Long. “We share information about what works and what doesn’t.” In 2021 JEA was honored with a first-place safety award from the American Public Power Association.
Fleet telematics improve driver safety at Shermco
With more than 800 trucks on the road providing electrical power maintenance, engineering, and testing solutions to clients, driver safety is a huge concern for Shermco. Jeremy Presnal, CSP and Vice President of EHS & Workforce Development first deployed technology to improve driver safety in 2015, with a product that restricted cell phone usage while driving. By 2020, he realized telematics could do much more.
Fleet safety software from Azuga highlights safe speeds and examines how drivers are braking and cornering. It can monitor idle time and track the location of vehicles. If drivers start to speed, or brake too hard, an audible alarm serves as a reminder to drivers to stay safe before there is an accident.
“We really liked the ability to assign all of our drivers a safety score,” says Presnal. “It allows us to showcase the many drivers who are doing it right every day.”
According to Presnal, as a result of the telematics solution, for the first time in five years, Shermco was able to achieve and maintain its corporate vehicle incident rate goal for the entire year.
Drivers initially had some trepidation at the system. The key to gaining acceptance was communicating how the information would be used. “We have intentionally not used the information as a disciplinary tool,” says Brian Borowczak, Director of Risk and Fleet Services for Shermco. “The message was “we’re doing it because we care about you.””
Safety is a core value at Shermco. “We are truly founded on being your brother’s keeper and keeping your co-workers safe,” says Presnal. “All employees are empowered to stop work if they see something that is not safe and we celebrate these events as learning opportunities and share across the organization." In addition, vehicle incidents are investigated, and lessons learned are shared across the fleet to help identify trends, opportunities, and improvements to minimize the risk of repeat incidents.
According to Presnal, drivers are now engaged in healthy competition based on their driver scores. The next step will be a gamification feature that will reward safe drivers. Before drivers get behind the wheel, they are trained on the Smith System, which Presnal believes is one of the best driver training programs in the industry. It focuses on five keys:
- Aim High in Steering
- Get the Big Picture
- Keep Your Eyes Moving
- Leave Yourself an Out
- Make Sure They See You
To access valuable safety resources, Presnal suggests contacting your insurance carrier and organizations such as the American Society of Safety Professionals (ASSP) Utilities Practice Specialty (UPS), the National Safety Council, and the Fleet Safety Leadership Council.
Subscribe to The Utility Expo monthly newsletter to receive more industry insights like this.
Read Next
Video: Preco Explains Its Radar-Based Collision Avoidance Tech at The Utility Expo 2021
Turn Safety Failure Into Success: Schlouch Inc's Tips for Building a Sustainable Safety Culture